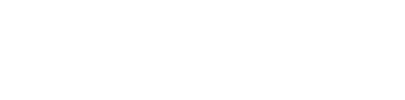


1目的
通过实施本制度,识别作业活动中的危险、有害因素,对其风险进行评估,提前分析、评估,从而制定风险控制措施,实现管理关口前移和源头管理,实现事前预防,达到减少危害、控制风险的目的。
2适用范围
本制度适用于公司内所有作业活动、设备设施和职业危害因素的风险管理。
3引用标准
《企业职工伤亡事故分类》 GB6441—86
《生产过程危险和有害因素分类与代码》 GBT13861-2009
《危险化学品从业单位安全标准化规范》 AQ/3013-2008
《危险化学品生产、储存装置个人可接受风险标准和社会可接受风险标准(试行)》安监总局2014年第13号公告
《化工企业安全风险分级管控实施指南》 (试用版) )。
《山东省人民政府关于修改山东省生产经营单位安全生产主体责任认定的决定》省政府令第303号
《山东省安全生产条例》省人大常委会二十五次会议
《山东省危险化学品安全管理办法》 (省政府令第309号) )。
《安全生产风险分级管控体系通则》(db37/t—2016 )。
《化工企业安全生产风险分级管控体系通则》(GB37/t2971-2017 ) )。
《山东省企业风险分级管控和隐患排查治理体系建设验收评定标准》 (试行)
4职责
4.1公司总经理是公司风险分级管理工作的第一责任人,担任公司安全风险分级管理领导小组组长,落实个人安全风险管理职责,督促各部门落实风险管理职责。
4.2各部门负责人是本部门风险分级管理推进建设的第一责任人,各部门风险评估小组组长,负责组织本部门作业活动、设备设施及职业危害因素的危害识别和风险评估,保证本部门各项风险点管理措施的落实。
4.3生产部组织有关部门对各部门识别的危险、有害因素进行评估。
4.4安全科负责风险分析评估工作的统一管理和监督,组织开展风险点识别和风险评估方法培训教育工作,制定公司风险评估标准,监督各部门和各级人员落实安全风险防控职责。
5.1风险评估的目的
根据公司设备设施和各项工作活动,选择分析对象,识别危险有害因素,评估其风险,对发现的事故隐患实施管理,识别重大风险,实施有效控制。
5.2风险评估范围:
2 )常规和异常活动。
3 )事故及潜在紧急情况
4 )进入工作场所的所有人员活动;
6 )作业场所设施、设备、车辆、安全防护用品;
7 )人为因素,包括违反安全操作规程和安全生产规程制度
8 )化工生产过程
9 )销毁、销毁、拆除、处置;
11 )公司周围的环境。
5.3风险评估的方法
5.3.1危险、有害因素识别、风险评估步骤
1 )识别作业活动中的危险、有害因素,应划分作业活动。 工作活动划分可以是生产流程阶段、地理区域、设备、工作任务、生产阶段、部门划分或上述方法的组合。 进入受限空间,储罐内部清洗作业、带压堵漏、搬运、机械泵机械装配操作、维护、改造、维修、药剂配制、采样分析、承包商现场作业、吊装等均为作业活动。
工作活动划分后,应按表5.3-1填写工作活动清单。
表5.3-1作业活动清单
单位:填写人:填写时间:审核人:否:
序列号
活动名称
工作活动内容
工作场所/地点
实施单位
活动频率
备注
d>(活动频率:频繁进行、特定时间进行、定期进行)
2)识别设备设施和管理活动的危险、有害因素可按下列顺序:
(1)厂址:地质、地形、周围环境、气象条件等;
(2)厂区平面布局:功能分区、危险设施布置、安全距离等;
(3)建构筑物;
(4)生产工艺流程;
(5)生产设备、装置、机械、电气、特殊设施(锅炉)等;
(6)作业场所:粉尘、毒物、噪声、振动、辐射、高低温等;
(7)工时制度、女工保护、体力劳动强度等;
识别危险、有害因素之前应先列出拟分析的设备设施清单,按表5.3-2填写。
表5.3-2 设备设施清单
单位: 填表人: 填表时间: 审核人: NO:
序号 | 设备名称 | 类别 | 所在部位 | 所属单位 | 是否特种设备 | 备注 |
5.3.2危险有害因素识别的方法
根据公司的生产性质、工艺特点以及管理实际,采用工作危害分析(JHA)和安全检查表分析(SCL)两种方法分别对作业活动、设备设施和管理活动进行危险有害因素辨识和风险评价;采用风险矩阵法(LSR)进行风险度分析。
1)工作危害分析(JHA)
从作业活动清单中选定一项作业活动,将作业活动分解为若干个相连的工作步骤,识别每个步骤的潜在危险、有害因素,然后通过风险评价,判定风险等级,制定控制措施。
工作危害分析的主要目的是防止风险排查人员受伤害,也不能使其他人员受到伤害,不能使设备和其他系统受到影响或损害。工作危害分析辨识危险有害因素,应按照表5.3-3填写《工作危害分析(JHA)记录表》。
表5.3-3 工作危害评价(JHA)记录表
单位: 岗位: 受控编号:
序号 | 作业 步骤 | 危险源或潜在事件(人、物、作业环境、管理) | 主要 后果 | 现有控制措施 | L | S | R | 评 价 级 别 | 管 控 级 别 | 建议新增改进措施 | 备注 | ||||
工 程 技 术 | 安 全 管 理 | 培 训 教 育 | 个 体 防 护 | 应 急 处 置 | |||||||||||
2)安全检查表分析(SCL)
分析人员针对拟分析的对象列出一些项目,识别与一般工艺设备和操作有关的已知类型的危险、有害因素、设计缺陷以及事故隐患,查出各层次的不安全因素,然后确定检查项目。再以提问的方式把检查项目按系统的组成顺序编制成表,以便进行检查或评审。
安全检查表编制的依据主要有:
(1)有关标准、规程、规范及规定;
(2)国内外事故案例和企业以往的事故情况;
(3)系统分析确定的危险部位及防范措施;
(4)分析人个人的经验和可靠的参考资料;
(5)有关研究成果,同行业或类似行业检查表等。
安全检查表分析可用于对物质、设备、工艺、作业场所或操作规程的分析,分析的对象是设备设施、作业场所和工艺流程等,检查项目是静态的物,而非活动,故此列出的检查项目不应有人的活动,即不应有动作。
用安全检查表分析危险有害因素时,既要分析设备设施表面看得见的危险有害因素,又要分析设备设施内部隐蔽的构件和工艺的危险有害因素。
安全检查表分析首先列出检查项目,再列出与之对应的标准以及不达标准可能导致的后果,还应列出现有控制措施,提出改进、改正、控制措施。
采用安全检查表进行风险分析评价,应按表5.3-4填写《安全检查表分析(SCL)记录表》。
表5.3-4 安全检查表评价(SCL)评价表
单位: 岗位: 受控编号:
序号 | 检查项目 | 标准 | 不符合标准情况及后果 | 现有控制措施 | L | S | R | 评 价 级 别 | 管 控 级 别 | 建议新增改进措施 | 备注 | ||||
工 程 技 术 | 安 全 管 理 | 培 训 教 育 | 个 体 防 护 | 应 急 处 置 | |||||||||||
5.4风险评价
5.4.1制定风险评价准则的依据
1)危险危害因素所具有风险规模的大小、严重程度、发生频率、持续时间;
3)消除或控制风险的技术难度、经济承受能力;
4)员工及相关方的关注程度;
5)行业的技术标准、设计规范,企业的安全管理标准和技术标准;
6)企业的安全生产方针和目标;
7)设备实施使用说明和技术要求;
8)有关合同中的相关规定。
5.4.2风险评价的准则
风险评价准则包括事件发生的可能性L、后果的严重性S和风险度R,其中风险度R是发生特定危害事件的可能性及后果的结合,取值为R=L×S,根据表5.4-1、5.4-2、5.4-3判定。
表5.4-1 事件发生的可能性(L)判断准则
等级 | 标 准 |
5 | 在现场没有采取防范、监测、保护、控制措施,或危险、有害因素的发生不能被发现(没有监测系统),或在正常情况下经常发生此类事故或事件 |
4 | 危险、有害因素的发生不容易被发现,现场没有检测系统,也未作过任何监测,或在现场有控制措施,但未有效执行或控制措施不当,或危险、有害因素经常发生或在预期情况下发生 |
3 | 没有保护措施(如没有防护装置、没有个人防护用品等),或未严格按操作程序执行,或危险、有害因素的发生容易被发现(现场有监测系统),或曾经作过监测,或过去曾经发生类似事故或事件,或在异常情况下发生过类似事故或事件 |
2 | 危险、有害因素一旦发生能及时发现,并定期进行监测,或现场有防范控制措施,并能有效执行,或过去偶尔发生危险事故或事件 |
1 | 有充分、有效的防范、控制、监测、保护措施,或员工安全卫生意识相当高,严格执行操作规程,极不可能发生事故或事件 |
表5.4-2 事件后果的严重性(S)判别准则
等级 | 法律法规及其他要求 | 人员伤亡 | 财产损失(万元) | 停工 | 公司形象 |
5 | 违反法律、法规和标准 | 死亡 | ≥20 | 全厂停工 | 省内影响 |
4 | 潜在违反法律、法规和标准 | 丧失劳动能力 | ≥10 | 车间部门级停工 | 行业内及市内影响 |
3 | 不符合上级公司或行业的安全方针、制度、规定等 | 截肢、骨折、听力丧失、慢性病 | ≥5 | 岗位级停工 | 县内影响 |
2 | 不符合公司的安全操作程序、规定等 | 轻微受伤、间歇不舒服 | <5 | 受影响不大,几乎不停工 | 公司及周边范围影响 |
1 | 完全符合 | 无伤亡 | 无损失 | 没有停工 | 形象没受损 |
表5.4-3 风险等级(R)判定准则及控制措施
风险度 | 等 级 | 应采取的行动/控制措施 | 实施期限 |
20~25 | 巨大风险 | 在采取措施降低危害前,不能继续作业,对改进措施进行评估 | 立刻 |
15~16 | 重大风险 | 采取紧急措施降低风险,建立运行控制程序,定期检查、测量及评估 | 立即或近期 整改 |
9~12 | 中等风险 | 可考虑建立目标、建立操作规程,加强培训及沟通 | 按照年度计划实施整改 |
4~8 | 可接受风险 | 可考虑建立操作规程、作业指导书,但需定期检查 | 有条件、有经费时治理 |
<4 | 轻微或可忽略的风险 | 无需采用控制措施,但需保存记录 |
5.4.3评价风险程度
1)风险评价由各单位分管领导组织安全员、设备员、技术员及相关人员根据国家和省相关文件标准进行评价,根据风险评价的结果划分出风险等级,编制车间级危险危害因素辨识和风险评价表,由单位负责人批准后实施,并上报公司安全部门。
2)安全部门根据各单位上报的车间级危险危害因素,组织有关人员进行最终评价,编制出公司控制的危险危害因素清单,并确定重大风险,在确定重大风险时,应考虑:
(1)法规、标准的要求。
(2)发生的可能性和后果的严重性。
(3)公司的声誉和社会关注程度等。
3)安全部门根据《危险化学品重大危险源辨识》(GB18218-2009)评价出公司级重大危险源,并编制重大危险源应急救援预案。
5.5风险控制
风险控制采用运行控制、设定目标管理方案进行控制、应急准备与响应程序进行控制及其他方法等。各单位都应当对重大风险制定、实施和保持相应的控制措施,包括工程技术措施、管理措施、培训教育措施和个体防护措施等,并与公司活动、员工水平、管理经验相适应。在选择风险控制措施时,应考虑:
1)控制措施的可行性和可靠性。
2)控制措施的先进性和安全性。
3)控制措施的经济合理性及经济运行情况。
4)可靠的技术保证和服务。
5.6风险评价信息更新
5.6.1危险危害因素辨识、风险评价实行动态管理,当发生以下变化时应及时进行辨识、评价和更新。
1)新的或变更的法律法规或其他要求实施;
2)操作条件变化、工艺改变或生产装置发生重大变化;
3)技术改造项目;
4)企业的生产经营范围及作业区域发生变化;
5)组织机构发生大的调整,或人员构成发生大的变化;
6)有对事故、事件或其它信息的新认识。
5.6.2相关部门应在出现情况后及时对相应的危险危害因素按要求进行重新识别评价。
5.6.3公司各级组织应按照《安全生产风险分级管控体系通则》(DB37/T—2016)要求每年对危险危害因素进行一次风险分析评价,风险分析记录和评价报告要上报生产部。发现事故征兆要立即发布预警信息,落实防范和应急处置措施。对重大危险源和重大隐患要报当地安全生产监管监察部门、负有安全生产监管职责的有关部门和行业管理部门备案。
5.6.4化工过程风险分析应包括:工艺技术的本质安全性及风险程度;工艺系统可能存在的风险;对严重事件的安全审查情况;控制风险的技术、管理措施及其失效可能引起的后果;现场设施失控和人为失误可能对安全造成的影响。在役装置的风险辨识分析还要包括发生的变更是否存在风险,吸取本企业和其他同类企业事故及事件教训的措施等。
5.6.5要按照《危险化学品重大危险源监督管理暂行规定》(国家安全监管总局令第40号)的要求,根据国家有关规定或参照国际相关标准,确定本企业可接受的风险标准。对辨识分析发现的不可接受风险,要及时制定并落实消除、减小或控制风险的措施,将风险控制在可接受的范围。
5.7风险评价的宣传教育和隐患治理
5.7.1有关部门应将风险评价的结果及所应采取的控制措施对从业人员进行宣传培训,使其熟悉工作岗位和作业环境中存在的危险、有害因素,掌握和落实应采取的控制措施。
5.7.2有关单位应对风险评价出的隐患项目,下达隐患整改通知书,责任单位应严格按照“五定”原则进行整改。
5.7.3在公司门口醒目位置设置风险公告栏,在存在安全生产风险的岗位设置岗位风险公示牌,分别标明本企业、本岗位主要危险点、危险等级、事故预防及应急措施、管控责任人和监督人等内容。
5.7.4在重大危险源、存在严重职业病危害的场所设置明显安全警示标志,并悬挂职业病危害因素告知牌,定期组织岗位人员进行检测,检测结果向岗位人员进行告知。
5.7.5在有重大事故隐患和较大危险的场所和设施设备上设置明显标志,标明治理责任、期限及应急措施。
5.7.6必须及时向员工公开安全生产行政处罚决定、执行情况和整改结果。
6、风险分级管控原则
5级:稍有危险,需要注意(或可忽略的)。员工要引起注意,各工段、班组员工负责5级危害因素的控制管理,需要控制措施的纳入蓝色风险监控。
4级:蓝色风险\轻度(一般)危险,可以接受(或可容许的)。有关车间负责4级危害因素的控制管理,所属工段、班组具体落实;不需要另外的控制措施,应考虑投资效果更佳的解决方案或不增加额外成本的改进措施,需要监视来确保控制措施得以维持现状,保留记录。
3级:黄色风险\中度(显著)危险,需要控制整改。公司、部室(车间上级单位)负责3级危害因素的控制管理,所属车间、科室具体落实;要制定管理制度、规定进行控制,努力降低风险,要仔细测定并限定预防成本,在规定期限内实施降低风险措施。在严重伤害后果相关的场合,必须进一步进行评价,确定伤害的可能性和是否需要改进的控制措施。
2级:橙色风险\高度危险(重大风险),必须制定措施进行控制管理。公司各分管领导对重大及以上风险危害因素要重点控制管理。当风险涉及正在进行中的工作时,要采取应急措施,并根据需求为降低风险制定目标、指标、管理方案或配给资源、限期治理,直至风险降低后才能开始工作。
1级:红色风险\不可容许的(巨大风险),极其危险,必须立即整改,不能继续作业。只有当风险已降低时,才能开始或继续工作。如果无限的资源投入也不能降低风险,就必须禁止工作,立即采取隐患治理措施,该风险由公司总经理负责。
以下情形应直接确定为2级风险:
违反法律、法规及国家标准中强制性条款的;
发生过死亡、重伤、重大财产损失的事故,且现在发生事故的条件依然存在的;
根据GB评估为重大危险源的储存场所;
运行装置界区内涉及抢修作业等作业现场10人及以上的;
7、风险控制措施
7.1 工程技术措施,实现本质安全;
7.2 管理措施,规范安全管理,包括建立健全各类安全管理制度和操作规程;完善、落实事故应急预案;建立检查监督和奖惩机制等;
7.3 教育措施,提高从业人员的操作技能和安全意识;
7.4 个体防护措施,减少职业伤害。
7.5 要求:在风险分级管控中,根据风险分析和生产实际情况,设备设施和作业活动已具备有关安全措施,能够满足安全生产要求的不在制定有关措施。
8、风险培训
公司各级单位要制定风险评估培训计划,组织员工对本单位的风险评估方法、评估过程及评估结果进行培训。
9、风险信息更新
公司各级单位要依据辨识评价结果,建立本部门的《风险点登记台账》(参照表9.1),台账应结合实际定期更新(每年至少一次)。
单位: 填表人: 填表时间: 审核人: NO:
序号 | 风险点名称 | 类型 | 风险等级 | 区域位置 | 管控部门 | 备注 |